Transforming the Future of Manufacturing with CNC Machining
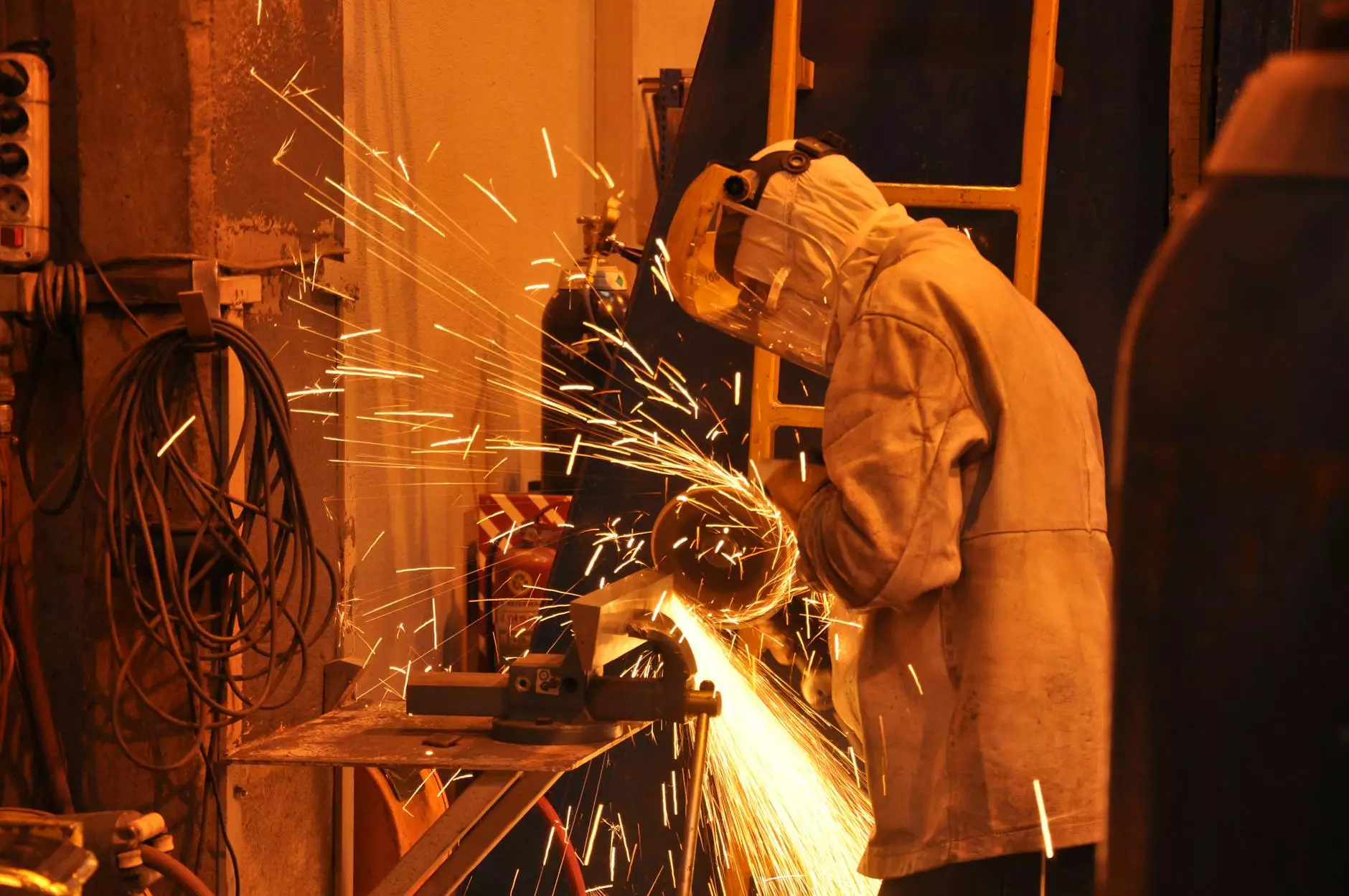
In the fast-paced world of manufacturing, the adoption of CNC machining has marked a significant turning point. Standing for Computer Numerical Control machining, CNC technology has revolutionized the way manufacturers approach production, offering unparalleled precision, efficiency, and flexibility. It is crucial for businesses in the realm of metal fabrication, such as Deep Mould, to understand the transformative potential of this technology.
What is CNC Machining?
CNC machining refers to the process of using computer-controlled machines to cut, shape, and fabricate materials into a desired design. The process begins with a digital design, often created using CAD (Computer-Aided Design) software. The CNC machine reads the design file and executes the cutting with precision. This technology can work with a variety of materials including metals, plastics, and composites, making it incredibly versatile.
How CNC Machining Works
The efficiency of CNC machining lies in its automated process. Here’s a step-by-step breakdown of how it works:
- Design Creation: The first step involves creating a detailed 3D model using CAD software. This model serves as the blueprint for the entire machining process.
- G-Code Generation: Once the design is complete, the CAD file is converted into G-code, a language that CNC machines can understand. This code contains all the instructions required for the machine to perform its tasks.
- Machine Setup: The CNC machine is set up according to the specifications outlined in the G-code. This may include selecting the right tools and adjusting the machine’s parameters.
- Machining Process: The machine begins the machining process, following the G-code instructions meticulously. It cuts, drills, and shapes the materials as specified.
- Quality Control: After the machining is complete, the finished product undergoes thorough inspection to ensure it meets all quality standards.
Benefits of CNC Machining
The rise of CNC machining has brought forth numerous advantages that have made it the go-to choice for many manufacturers, particularly in the metal fabrication industry. Here are some key benefits:
- High Precision: CNC machines deliver an extraordinary level of accuracy, with tolerances often within a thousandth of an inch. This precision is vital in industries requiring detailed specifications.
- Consistency and Reproducibility: Once a CNC machining program is created, it can be reused time and again, ensuring that each part produced is identical to the first.
- Operational Efficiency: CNC machines can operate continuously without the need for breaks, significantly increasing overall productivity.
- Design Flexibility: With CNC machining, complex designs can be easily produced without the need for specialized tooling or setups.
- Reduced Labor Costs: As the machines take over the labor-intensive tasks, human employees can focus on more strategic roles, thereby reducing labor costs and increasing efficiency.
Applications of CNC Machining
The applications of CNC machining span across various industries, making it a cornerstone of modern manufacturing. Some prominent applications include:
- Aerospace Manufacturing: CNC machining is extensively used to manufacture complex aircraft components with high precision and reliability.
- Automotive Industry: Many automotive parts, including engine components and transmission systems, are produced using CNC technology.
- Medical Equipment: The medical field benefits from CNC machining for creating intricate devices and prosthetics, where precision is critical.
- Electronics: From casings to circuit boards, CNC machining is vital in the production of electronic components.
- Furniture Design: Unique furniture pieces can be crafted using CNC machining, allowing for intricate design work that traditional methods cannot achieve.
Challenges and Considerations in CNC Machining
While the benefits of CNC machining are significant, there are also challenges that manufacturers face. Understanding these can help businesses like Deep Mould navigate the landscape more effectively.
- Initial Investment: The cost of CNC machines can be substantial, and small businesses may face hurdles in initial investment.
- Complex Programming: While CNC machines are efficient, the programming requires a skilled technician familiar with G-code and CAM (Computer-Aided Manufacturing) systems.
- Material Limitations: Certain materials pose challenges due to their hardness or brittleness, affecting the type of tools required for machining.
The Future of CNC Machining
The trajectory of CNC machining is pointing towards an exciting future. As technology continues to evolve, several trends are shaping the landscape:
- Integration with AI: Artificial intelligence is poised to enhance CNC machining by optimizing processes, predicting maintenance needs, and improving production efficiencies.
- 3D Printing Synergy: As additive manufacturing grows, the integration of CNC machining with 3D printing technologies will create hybrid solutions that can produce more complex geometries.
- Increased Customization: Customers are increasingly demanding bespoke designs, and CNC machining provides the flexibility to accommodate these needs rapidly.
- Smart Manufacturing: The rise of the Internet of Things (IoT) will allow for smarter factories, where CNC machines communicate and share data for improved efficiency.
Why Choose Deep Mould for CNC Machining?
As a leader in the metal fabrication industry, Deep Mould harnesses the power of CNC machining to deliver top-notch manufacturing solutions. Here’s why choosing Deep Mould could be advantageous for your business:
- Expertise: With years of experience in the industry, our skilled professionals bring unmatched expertise to every project.
- Advanced Technology: We utilize state-of-the-art CNC machines to ensure that all products meet the highest quality standards.
- Customized Solutions: At Deep Mould, we understand that every client has unique needs. We offer tailored solutions that cater to specific requirements.
- Commitment to Quality: Our rigorous quality control processes guarantee that every item leaving our facility meets international quality benchmarks.
- Timely Delivery: We believe in respecting our clients’ timelines and ensure prompt delivery of all projects.
Conclusion
In conclusion, CNC machining is not just a manufacturing process; it is a vital technology that is transforming industries. The ability to achieve high precision, efficiency, and flexibility makes it an invaluable asset in modern manufacturing. As companies like Deep Mould continue to innovate and refine their CNC machining capabilities, the future of manufacturing is brighter than ever. By embracing this technology, businesses can enhance their production processes, meet customer demands, and ultimately, thrive in an increasingly competitive market.