Understanding Stereolithography: Revolutionizing 3D Printing
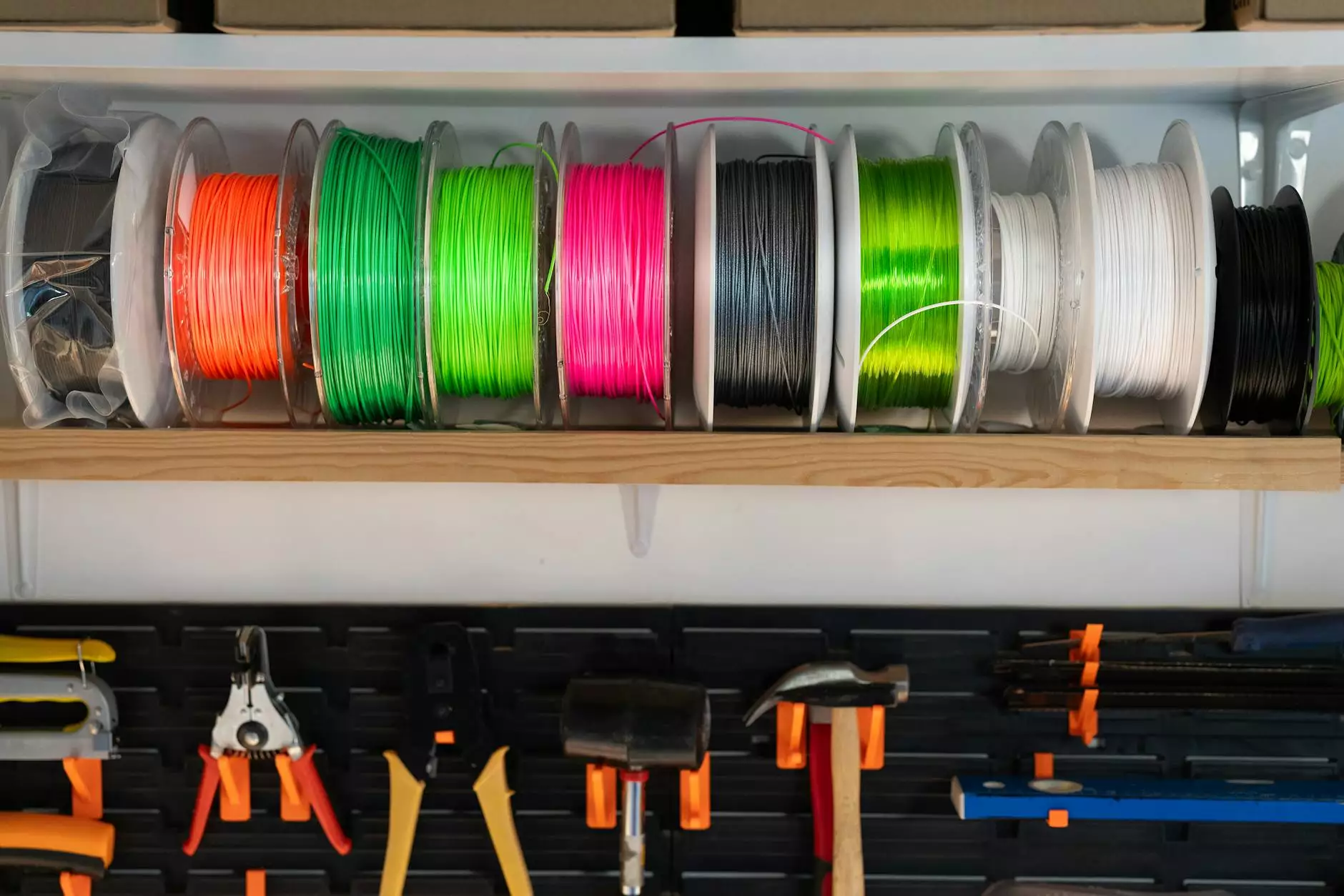
In the rapidly evolving world of manufacturing, stereolithography (SLA) stands out as a pioneering technology that has significantly impacted the field of 3D printing. This process, which was invented in the early 1980s by Chuck Hull, has transformed the way products are designed, developed, and produced. In this comprehensive article, we explore the intricate details of stereolithography, its processes, applications, benefits, challenges, and future prospects.
What is Stereolithography?
Stereolithography is a 3D printing technology that utilizes a laser to cure liquid resin into hardened plastic. It is one of the earliest forms of 3D printing and is known for its ability to produce high-resolution parts with intricate details. The basic principle involves the layer-by-layer addition of material, allowing for the creation of complex geometries that would be difficult or impossible to achieve through traditional manufacturing methods.
How Stereolithography Works
The stereolithography process consists of several critical steps:
- Design Phase: The process begins with a 3D model created using Computer-Aided Design (CAD) software. This model is then exported in a format compatible with the stereolithography printer.
- Slicing: The 3D model is sliced into thin horizontal layers, which the printer will build one at a time. This slicing software determines how each layer will be printed and is essential for achieving high fidelity in the final part.
- Printing: The SLA printer uses a UV laser to selectively cure the liquid resin. As each layer is completed, the platform holding the part moves down into the resin bath to allow the next layer to be formed.
- Post-Processing: Once the print is complete, the part is removed from the printer and typically undergoes rinsing in a solvent to remove uncured resin, followed by UV exposure for additional curing.
The Advantages of Stereolithography
Stereolithography offers numerous advantages that make it a preferred choice in various industries:
- High Precision: SLA is known for its exceptional accuracy and surface finish, making it ideal for applications that demand fine details.
- Complex Geometries: The layer-by-layer approach allows for the production of complex shapes, including intricate designs that traditional methods struggle to achieve.
- Material Variety: Advances in resin formulations have led to a wide range of materials that can be used in SLA, including flexible, durable, and heat-resistant options.
- Rapid Prototyping: SLA enables rapid creation of prototypes, significantly speeding up the design and testing phases of product development.
Applications of Stereolithography
The applications of stereolithography are vast and span across multiple industries, including:
Aerospace
In the aerospace sector, SLA is often used for creating lightweight, complex parts that meet strict performance standards. The ability to prototype and test components quickly allows for faster innovation in aircraft design.
Medical
The medical industry benefits significantly from SLA in the production of custom implants, prosthetics, and surgical guides. The precision of stereolithography allows for tailored solutions that improve patient outcomes.
Automotive
Automotive manufacturers utilize stereolithography for creating prototypes and parts that test form, fit, and function. The speed of production aids in achieving tighter design cycles, ultimately leading to more efficient vehicle production.
Consumer Products
From jewelry to household items, SLA enables designers to produce unique, customized consumer products. The capability to quickly iterate designs meets the growing market demand for personalized items.
Challenges in Stereolithography
While stereolithography presents numerous benefits, there are also challenges associated with this technology:
- Material Limitations: Although the range of available resins is expanding, some materials may not meet all performance requirements for specific applications.
- Post-Processing Requirements: The need for extensive post-processing can add time and costs to the production cycle, which may not be ideal for all businesses.
- Cost of Equipment: High-quality SLA printers can be expensive, and while prices have decreased over time, initial investment can be a barrier for small businesses.
The Future of Stereolithography
The future of stereolithography looks promising as technology continues to evolve. Advances in materials science are paving the way for new resin formulations that enhance mechanical properties and expand applications.
Furthermore, innovations in printer technology are reducing costs and increasing accessibility for smaller firms. As more businesses recognize the potential of SLA, its adoption is likely to grow, fostering a new era of design and production.
Conclusion
In conclusion, stereolithography remains a cornerstone of 3D printing technology, providing solutions that cater to a myriad of industries. With its ability to produce complex, high-quality parts quickly and efficiently, it is no wonder that stereolithography continues to shape the future of manufacturing. As we look towards the future, the integration of SLA into mainstream production processes will only continue to enhance innovation. Embracing this technology can yield significant competitive advantages for businesses looking to innovate, improve efficiency, and meet the demands of modern consumers. For more information and to explore our offerings in 3D printing, visit infotron.com.tr.